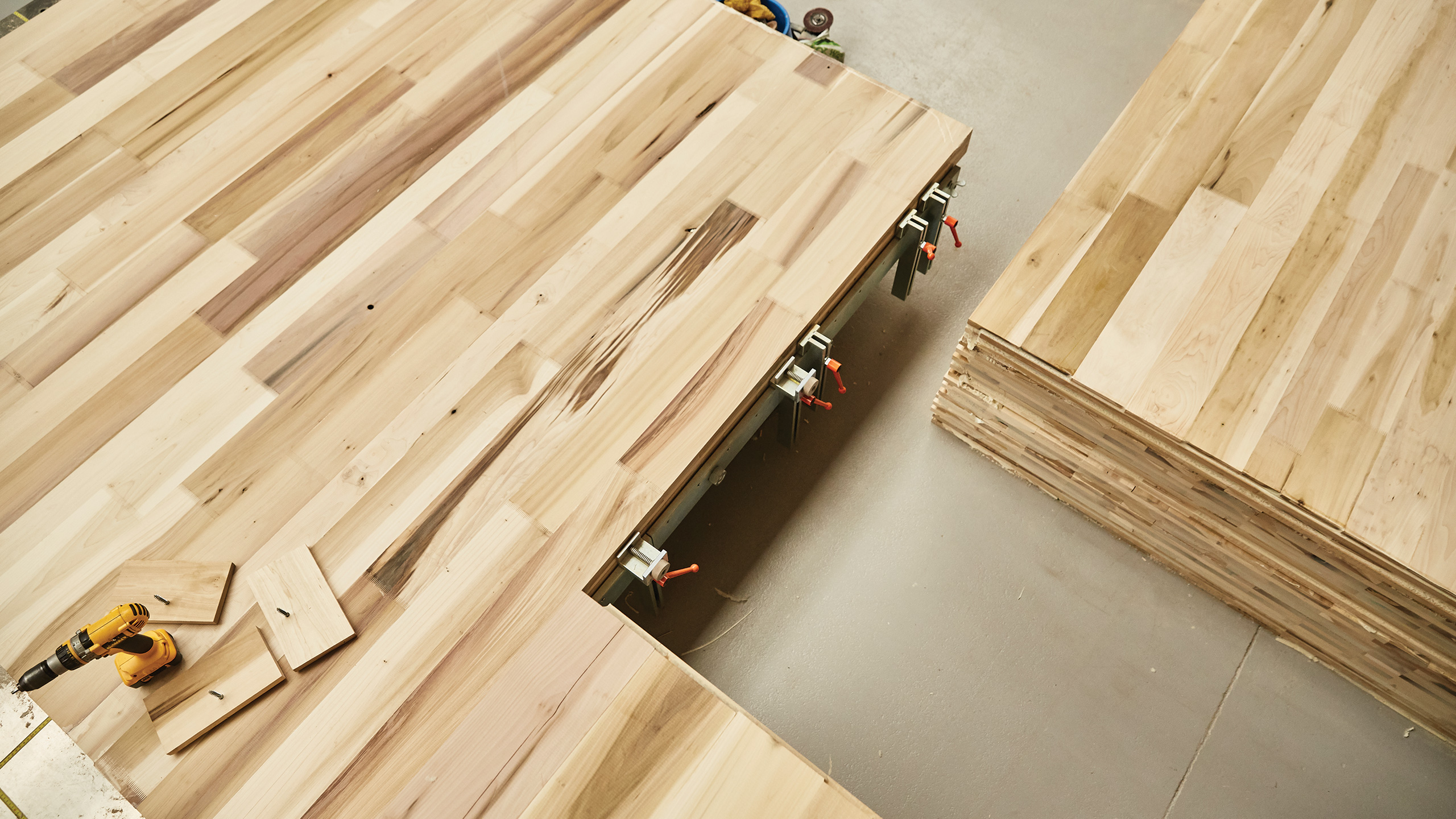
Most Scottish home building is currently open, single sheathed and closed panel timber-frame, but more construction companies are evaluating use of solid laminate timber systems, most notably CLT. CSIC has consequently developed its knowledge base and facilities to support them. MultiPly took that process further.
“Until AHEC approached us, all our work had largely utilised home-grown or imported softwood,” said Mr Milne. “In fact, this has been the first time large-scale hardwood CLT panels have been made in the UK, where actually there’s no-one yet manufacturing CLT in any volume at all. Like other CLT users in this country, AHEC had to have it manufactured for previous projects, like the tulipwood Smile installation at the 2016 London Design Festival, elsewhere in Europe.”
CSIC’s brief was firstly to make the finger-jointed, planed lamellas from Glenalmond into panels for testing at Edinburgh Napier University, then the core 101 CLT panels, split approximately 50/50 between three-ply 60mm and five-ply 100mm thicknesses, for the MultiPly pavilion itself, and lastly, an additional nine panels, 4 of which were fabricated using ultra-durable, moisture resistant thermally-modified tulipwood. These were for fabricating stages and modular venues for a day of special events on Exhibition Road, organised as part of the London Design Festival, throughout which MultiPly itself will feature as an installation in the V&A Museum.
Given tulipwood’s hardness and lower porosity compared to softwood, CS-IC liaised closely with Henkel, manufacturer of the Purbond PUR adhesive used on the panels.
“They advised us to apply the adhesive at 170gm/m2, compared to the 130-150gm/m2 typically used for softwood CLT, and to double press time to five hours,” said Mr Milne. “They also recommended that all glued surfaces be treated with a primer solution designed for use with PUR. This opened up the timber for the adhesive and the wetting involved also helped as the tulipwood came to us at 8%/9% moisture content, the lower limit for using PUR. It was all a valuable learning process and gives us the basis for further research into use of hardwood in engineered timber.”
To ensure consistency and validate the gluing approach, he added, CSIC also sent factory production control samples to Henkel for delamination testing. They passed. While CSIC’s press can make panels up to 13.5mx3.5mx400mm, those for MultiPly were all 2.7mx2.7m due to the modular design of the building. Among key outcomes of the project for the Centre were its demonstration of the superior stiffness and strength to weight of tulipwood, which lend it naturally to CLT production.
“The high profile of MultiPly, on display in such a prestige venue as the V&A, could also add to momentum for the start of commercial CLT manufacture in the UK,” said Mr Milne. “We believe it can only be a matter of time.” Professor Robert Hairstans, head of COCIS, agrees that MultiPly could open up new horizons for CLT, and not just in the UK.
The role of COCIS in the project was to undertake exhaustive performance testing of the timber and finished panels. Like CSIC, it works across all types of building materials, but given the nature of the industry in Scotland, timber-based building, notably allied with offsite and modern methods of construction, is similarly a core research field.
“On MultiPly we initially worked with Glenalmond on characterising the raw material to ensure it was fit for purpose,” said Professor Hairstans. “We then ran further tests after defect cutting and finger jointing. We were aware of the use of tulipwood CLT in AHEC’s The Smile and in the new Maggie’s Centre in Oldham, but there were still unknowns, particularly about the finger jointing process. However, the joints performed well and, together with the defect cutting, produced very clean, clear panels.”
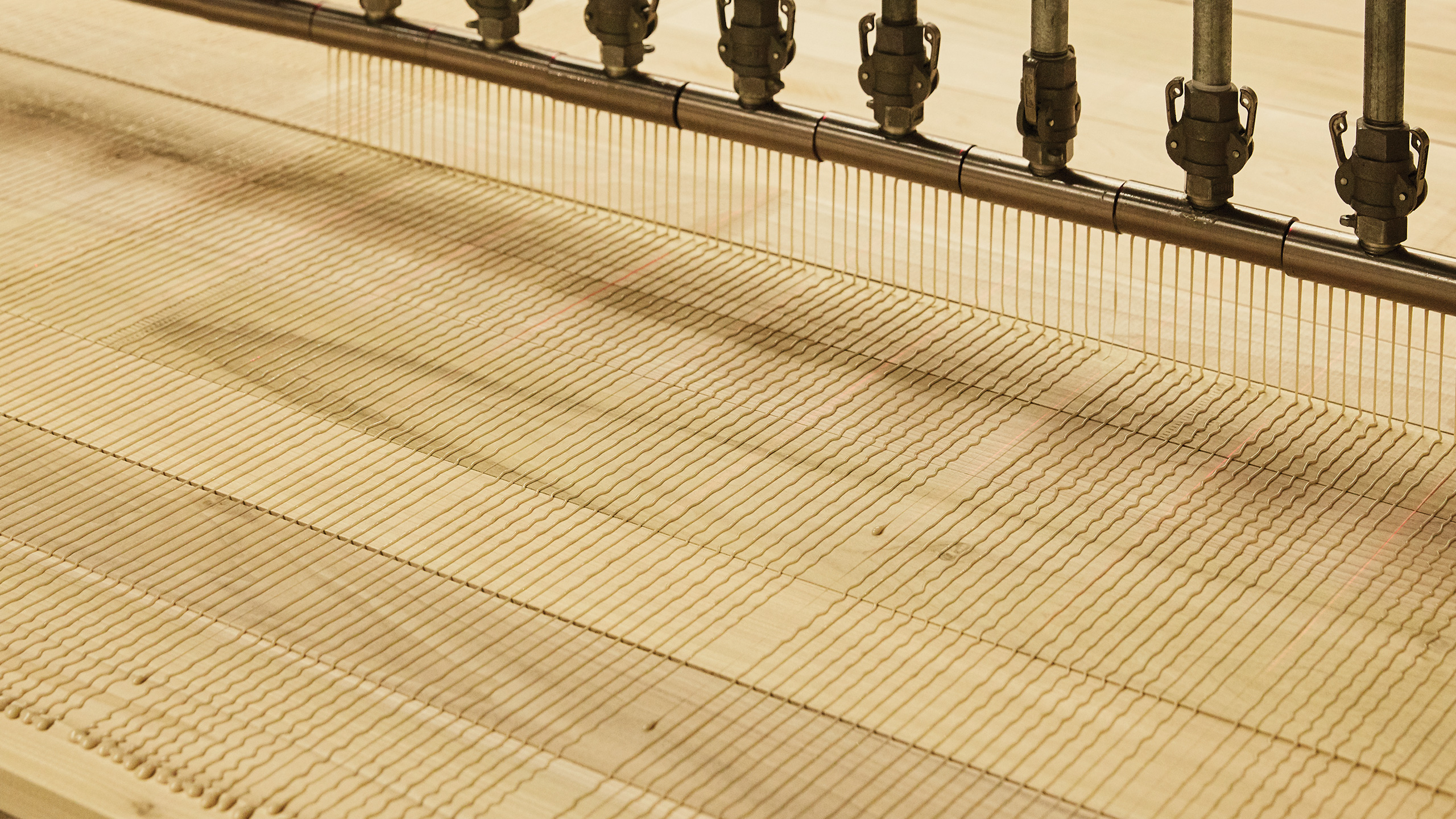
The aesthetics of the tulipwood panels, he agreed with Mr Milne, should catch the eye of designers and architects. “You’d want to keep as much as possible on show,” he said. “It would be criminal to cover it up with plasterboard!”
The next step for the COCIS was evaluation of the finished panels in line with European standards to allow design conformity with EuroCode 5. This involves shear testing and assessment of mechanical performance flat-wise for flooring panels, and edgewise for those standing vertically and spanning openings. At the time of going to press, some tests were still ongoing. However Professor Hairstans didn’t ‘envisage failure’.
Once complete, COCIS will publish its findings from the project. “From Edinburgh Napier’s perspective we want our work to have impact and in this instance that would ultimately mean uptake of tulipwood in CLT manufacture,” said Professor Hairstans. “Our core theme will be the possibilities for integrating tulipwood into CLT production and the nature of the end product; one with a high strength to weight ratio and pleasing aesthetics, so with good engineering and architectural credentials. We’ll also expand on the material’s mechanical properties and what it could achieve in different building typologies.”
Edinburgh Napier sees potential too for sharing its work on MultiPly with partner universities in the US, where CLT production is becoming increasingly established and where it sees ‘real scope for uptake of tulipwood’.
Professor Hairstans additionally maintained that tulipwood CLT’s technical merits and carbon and wider sustainability credentials can tie it into the drive to improve construction’s green credentials and ‘industrialise the way we deliver the built environment’, including through offsite and modular construction.
He and Mr Milne also highlighted that they got Edinburgh Napier Built Environment Exchange (beX) students involved in MultiPly materials testing and panel manufacture. It was partly that they needed ‘all hands on deck to get the work done’. But it was also seen as valuable to involve future construction market shapers in an area of such innovation and development potential.
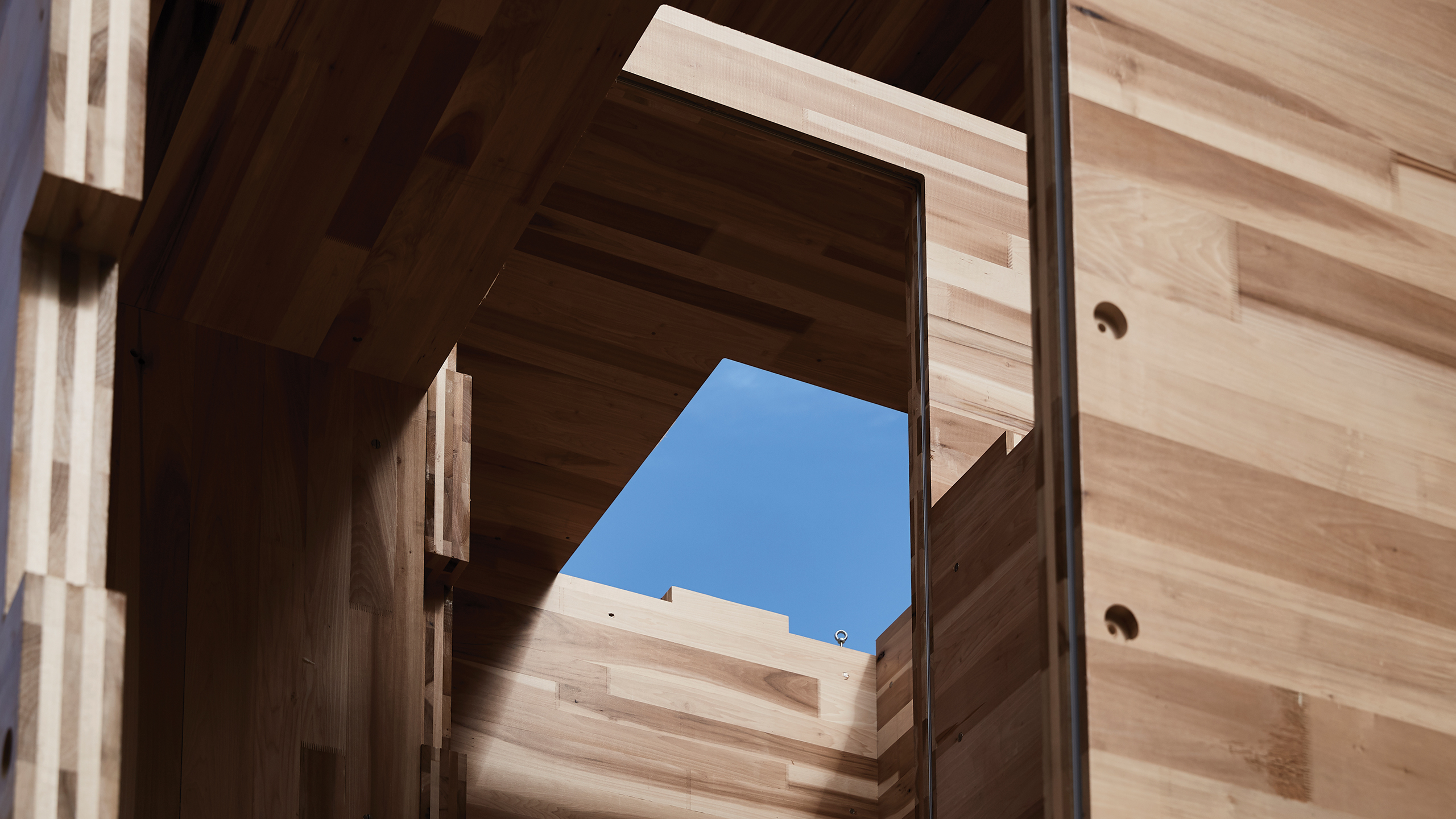