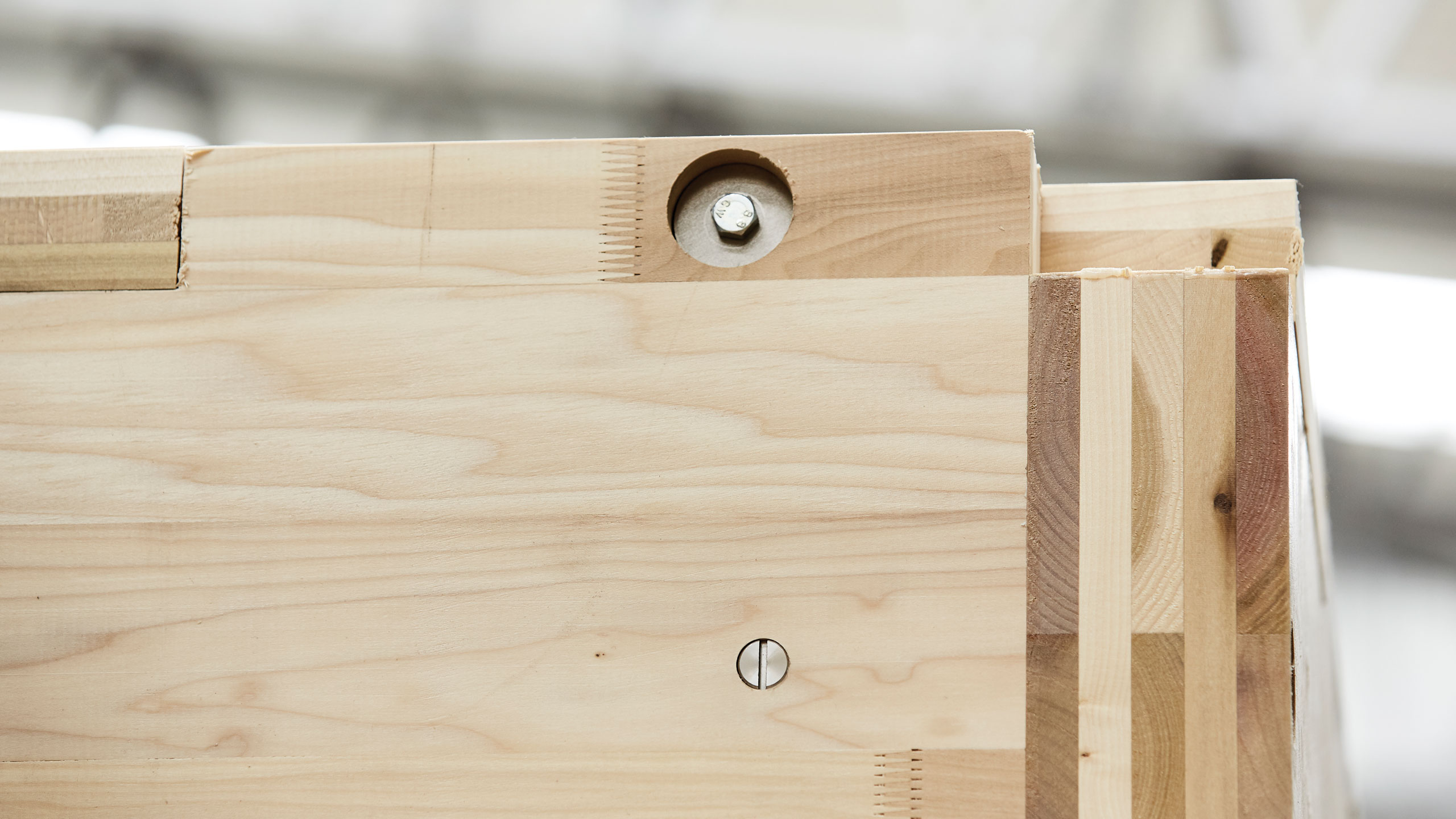
“The modern screws we used for The Smile were incredibly strong, but not best suited to disassembly,” said Bateman. “For MultiPly we wanted to explore the potential of accurately computer machined joints to create a demountable structure that could be quickly taken apart and reassembled.”
Arup was also engineer for the refurbishment of the Victoria and Albert Museum’s Sackler Courtyard, where MultiPly will be on show during the LDF, so it had in-depth knowledge of the constraints the site imposed. As the courtyard floor is also the roof of new galleries below, the key was not to overload it.
“The strength of the roof informed the height and massing of MultiPly,” said Carolina Bartram, Associate Director at Arup and who has been in charge of both projects. “But the fact that tulipwood has a high strength to weight ratio meant the installation could be relatively large, yet still light enough for the roof to safely support.”
The strength and stiffness of tulipwood has also allowed MultiPly’s other design features; the small bearing areas and slim panels, which would not have been possible in softwood. For exposed structures, maintains Arup, the American hardwood also offers significantly improved appearance.
Lawrence says MultiPly has reinforced his view that there’s potential for more application of hardwoods generally in construction. “As the use of timber increases, it’s important we maximise use of all our available species including hardwoods, which form a third of northern temperate forests,” he said. “With simple heat treatment, temperate hardwood can also match the durability of some of the best rainforest timbers. In fact, MultiPly is the first ever structure to incorporate thermally modified wood into some of its panels.”
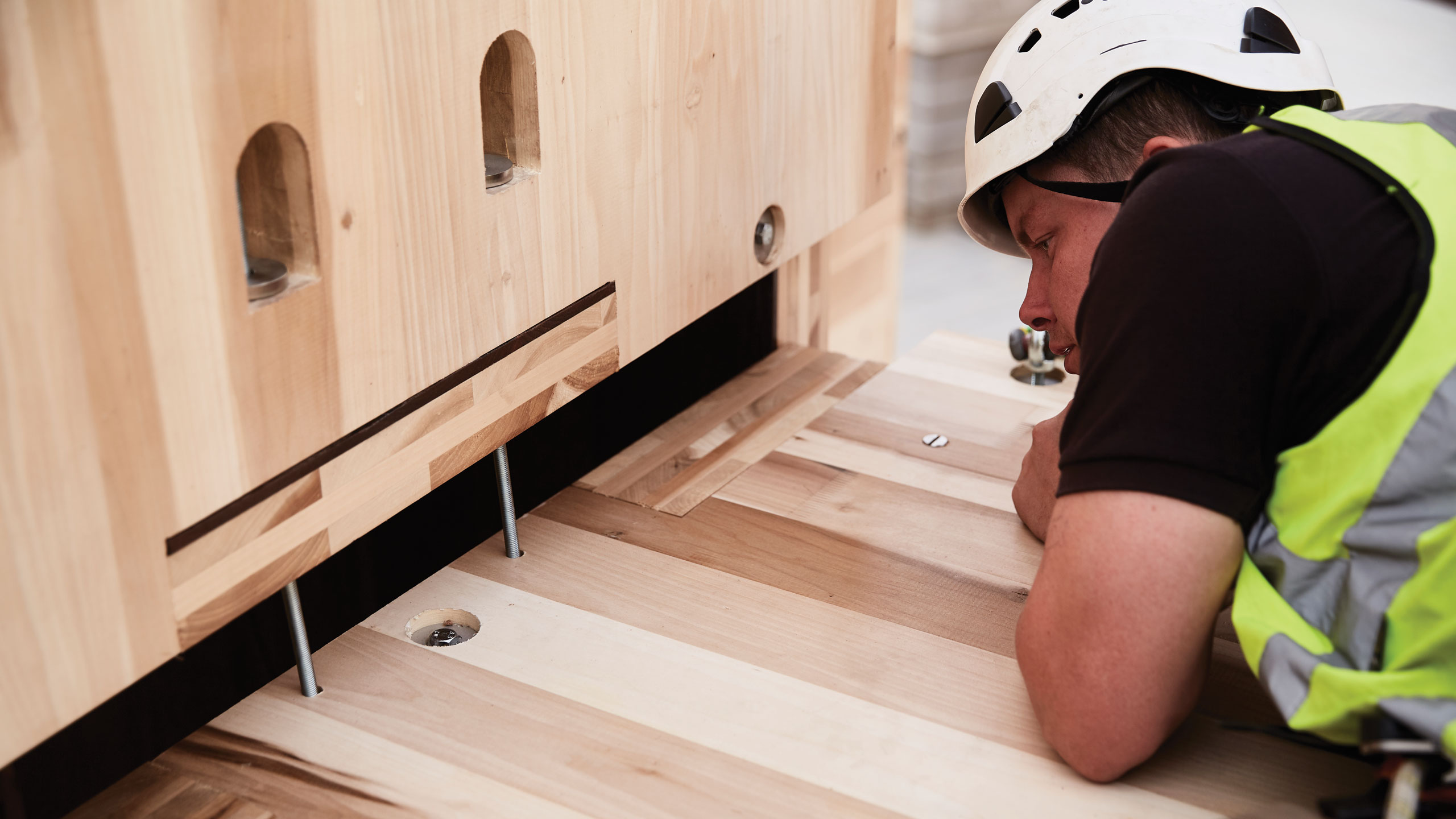
Arup is now exploring use of wood in a large number of its projects, with computer fabrication, CLT and new stronger cheaper connections enabling it to compete for an ever wider range of building types.
“It also has the advantage of being our only renewable construction material and can be self-finishing, combining structure and finishes into a single element,” said Lawrence.
Timber uptake in building, maintains Arup, is also being boosted by growth in prefabricated offsite construction.
“And CLT is particularly well suited to offsite as the panels can be CNC machined to very tight tolerances, while more sophisticated digital methods enable us to accommodate ever greater variety of geometries and typologies,” said Bartram. “MultiPly really demonstrates CLT’s potential in this market. Stage One will erect it in just six days and every piece of CLT has been used, with door cut outs, for instance, turned into stairs.”
Through the partnership of structural wood specialist Glenalmond Timber, which did the initial processing of the tulipwood, the Construction Scotland Innovation Centre, which made the CLT, Edinburgh Napier University’s Centre for Offsite Construction and Innovative Structures, which tested the panels and Stage One, which machined them, MultiPly also holds out the prospect for CLT manufacture in the UK.
“Part of our wish has been to help build local capacity in the UK timber sector and MultiPly does indeed use the first ever CLT panels made in the UK,” said Lawrence. “It’s an exciting moment, showing the UK is prepared to invest to be part of the global timber revolution. Better still, it’s in the UK engineering tradition of working with specialist high quality products, such as hardwoods.”